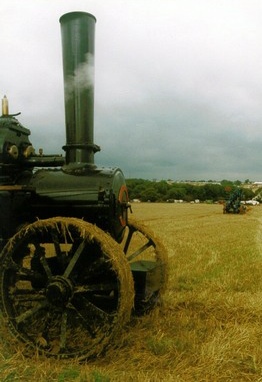
Between 1830 and 1850 patents describing steam cultivating machinery were numerous. Probably the most noteworthy innovators being John Heathcoat of Tiverton, Lord Willoughby de Eresby and the Marquis of Tweeddale. In 1854 the Royal Agricultural Society of England (RASE) offered a prize of £500 for “the steam cultivator which shall in the most efficient manner turn over the soil and be an economical substitute for the plough or spade”. The first contest took place at the Society’s summer meeting in Carlisle in 1855, and was repeated at Chelmsford in 1856 and Salisbury in 1857, without an award being made. The judges however awarded a medal to John Fowler as a reward for his strenuous endeavours, adding, “Steam ploughing as such had attained a degree of excellence comparable in point of execution with the best horse work.”
John Fowler Jnr (1826-64) had become prominent in the development of land cultivation machinery since he introduced his mole plough at the RASE meeting held in Exeter in 1850. A member of a leading Quaker family he had resolved as a young man to devote his time and resources to the cheapening of food production since witnessing at first hand the horrors of the Irish potato famine in 1845. After years of experimentation he competed at the RASE trials held in Chester in 1858, competing against Thomas Rickett’s rotary steam cultivator; Charles Burrell’s direct traction plough, fitted with James Boydell’s Endless railway wheels, and William Smith’s roundabout system. This was manufactured and entered by James and Frederick Howard of Bedford.
The judges kept Fowler waiting until the autumn of 1858 before announcing that he had been judged the winner, their report adding “It is beyond question that Mr. Fowler’s machine is able to turn over the soil and in an efficient manner at a saving compared with horse labour; while in all cases it is left in a far more desirable condition and better adapted for all the purposes of husbandry. We are unanimously of the opinion that he is fully entitled to the prize of £500.” The successful prize winning tackle employed a 10 nhp portable engine manufactured by Ransomes of Ipswich and suitably modified to accommodate a patent twin drum windlass, manufactured by Robert Stephenson of Newcastle-upon-Tyne, mounted under the engine smokebox. The anchor carriage on the opposite headland was designed by Jeremiah Head of Ransomes, and manufactured by Stephenson. The arrangement allowed the engine to draw the implement backwards and forward across the field, allowing the combined engine and windlass to wind itself along the headland at the end of each pull of the implement.
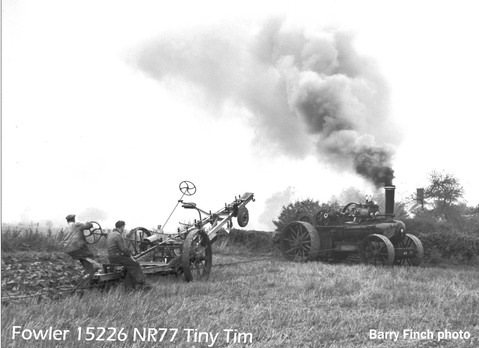
Further developments of both engines and implements followed quickly in the wake of his success at Chester. Firstly, a self-moving engine was developed and by the mid-1860s double engine tackle had been introduced with a self-moving engine working along each headland. Sadly, Fowler died in 1864 following a hunting accident, but his brother, Robert, and a competent team of colleagues continued his work. The most notable of these was David Greig, a Scot, who is credited with the development of the balance plough. The idea had been originally patented by the Fisken Brothers, in 1885, but Greig suggested a frame mounted as a “see-saw” carried on a two-wheeled axle, one side carrying the right-hand plough bodies and the other side the left hand, thus enabling the plough to turn all the furrows in the same direction by alternating the bodies. The first plough was built by Ransomes and tested at their works in Ipswich. In 1865 steerage was added to the plough. In 1884 the anti-balance plough was introduced overcoming the tendency of the plough to lift out of the ground in light soil owing to the weight of that half of the plough which was elevated and not at work. Greatly superior steel plough ropes were developed and for a time, Richard Burton’s ingenious clip drum was popular.
By this time the name Fowler was at the forefront wherever steam powered land cultivation was undertaken, especially in the developing countries of Eastern Europe. Other significant engine and tackle, manufacturers were Aveling & Porter of Rochester; J & H McLaren of Leeds; Charles Burrell of Thetford and J & F Howard of Bedford. Their combined output fell far short of that achieved by John Fowler.
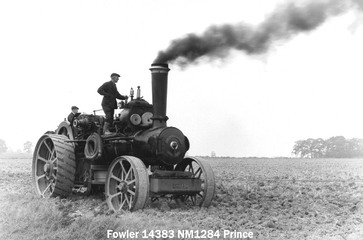
Contract ploughing
After 1865 most steam ploughing and cultivation was undertaken by steam ploughing contractors. Many farmers, other than the largest landowners, found the initial cost too high to justify investment. The travelling contractors were a unique breed. Each set of tackle usually comprised four men and a boy living together in a living van which travelled with the engines, implements and water cart.
Many engines spent time in the ownership of ploughing contractors. Most surviving BB1 class engines were part of a very large order placed by the Agricultural Machinery Board, a branch of the Ministry of Munitions, in the First World War to ensure the supply of ploughing engines to counter the German submarine menace. John Fowler & Company supplied over 140 type BB1 engines, together with balance ploughs, cultivators, water carts and living vans.
Improved soil management
The economic case for cable/steam cultivation was given in a paper before the British Association by David Greig in September 1867:
The steam engine stands on the headland and hauls the implement to and fro by means of a wire rope. All treading and compression of the soil and sub-soil associated with horse cultivation is thereby entirely avoided and the implement is driven at a much more rapid pace, throwing up the soil to a greater depth and in a loose state enabling it to derive full benefit from the influences of the atmosphere. In horse ploughing the case is just the reverse, for the sole of the plough and the treading of the animals so consolidates the bottom that the necessary chemical action between soil and sub-soil, and consequently all escape of gas and water is prevented.
The person who farms by steam has a powerful and untiring force at this disposal such that he can afford to wait until his land is in an exact state for working.
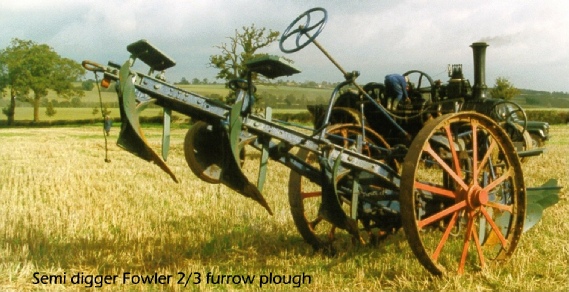